Reballing BGAs is a fairly efficient way to address several issues when it comes to semiconductors. For instance, you probably have poor solder joints if your screen occasionally goes black. Additionally, you can see horizontal or vertical dots on the screen, which is another indication of faulty solder joints. These problems can be solved via BGA reballing. Continue reading to see why BGA reballing is something you should think about doing if your PCB is damaged or torn.
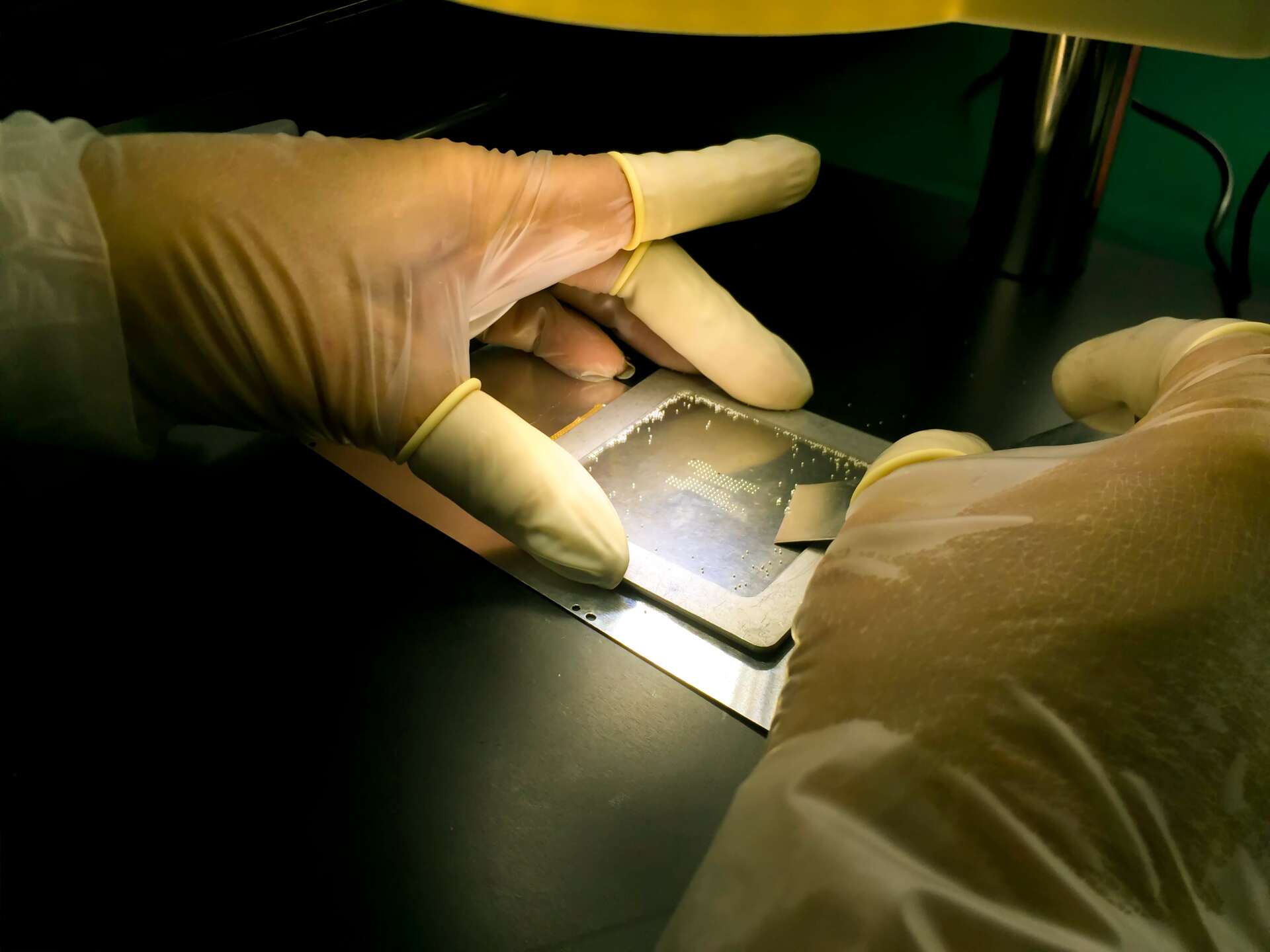
BGA Reballing Solder Spheres
Replacing the solder spheres on BGA packages is known as reballing. The procedure is manageable for a novice repairman. It doesn't need special frames or fixings. Additionally, it does away with the necessity to prepare equipment for reballing. After soldering, the finished object can be cleaned with alcohol. When reballing your BGA components, there are several things to take into account.
Deballing is the first stage in the three-step reballing procedure, which is then followed by the implantation of solder spheres. The solder spheres are then dissolved using a robotic solder dip system, which employs a gentle and regulated multi-unit procedure. Solder wicks, which could damage the pads, are not required with the automated procedure.
The numerous pins and challenging soldering of a BGA package lead to subpar performance and shaky connections. Reballing balls on the BGA grid frequently solves the connection-loosening issue. Solder spheres on the BGA package can aid in joining two packages together. A BGA reballing procedure is a precise procedure that needs precise management.
Testing
BGA reballing comes in two varieties. In the mechanical case, solder joints must be inspected using destructive techniques to see if they can endure stress. The other method, electrical, is mounting the BGA on the PCB and then passing current across it. Sadly, although electrical testing can assist in locating any electrical issues, it is unable to find physical faults on the BGA. Therefore, if you're thinking of BGA reballing for your next electronic component, you must combine the two techniques.
To ascertain whether the process was effective, the mechanical test is essential. Fractures in the solder and NI/intermetallic interface can result from mechanical stress. To lower the chance of defects, it is crucial to make sure the process is complete and under control. Utilising the most recent testing methods to guarantee a high-quality product is essential to avoid this issue.
Solder Bridges
Two solder depots may fuse during the reballing process, creating a bridge. These bridges can only be found with an X-ray inspection because they are not visible from the surface. When they are found, you need to uninstall the component and reinstall it to fix them. While BGA reballing, there are a few approaches to lessen the possibility of solder bridges.
Frowning, in which we compress the ball edges to the point where they come into contact with one another during the reflow, is one of the most frequent reasons for solder bridging. You may prevent this by maintaining minimum standoff heights with precision spacer blocks. For more information on how these spacers can assist you in removing solder bridging from BGA devices, refer to the Alpha TrueHeight Spacer Block product guide.
Using endoscopes is another technique for examining solder junctions. This device, which was first created for medical applications, is great for looking at little items that are crammed together. The inside row of connections and the outer row of connections can both be seen by technicians using this high-magnification tool, which frequently includes visualisation software. As a result, they can assess a solder joint's general quality and check for adequate reflow.
Give our specialists at M-Tek Assembly Ltd a call at 01189 455377 if you have any questions regarding BGA reballing or require it for your next projects. You will also be doing your part to protect the environment by utilising M-Tek for your
BGA reballing. We use electric vehicles to achieve a net-zero carbon footprint, and for every circuit board we produce, a tree is planted.
Follow us on Twitter to stay up to date on our services.