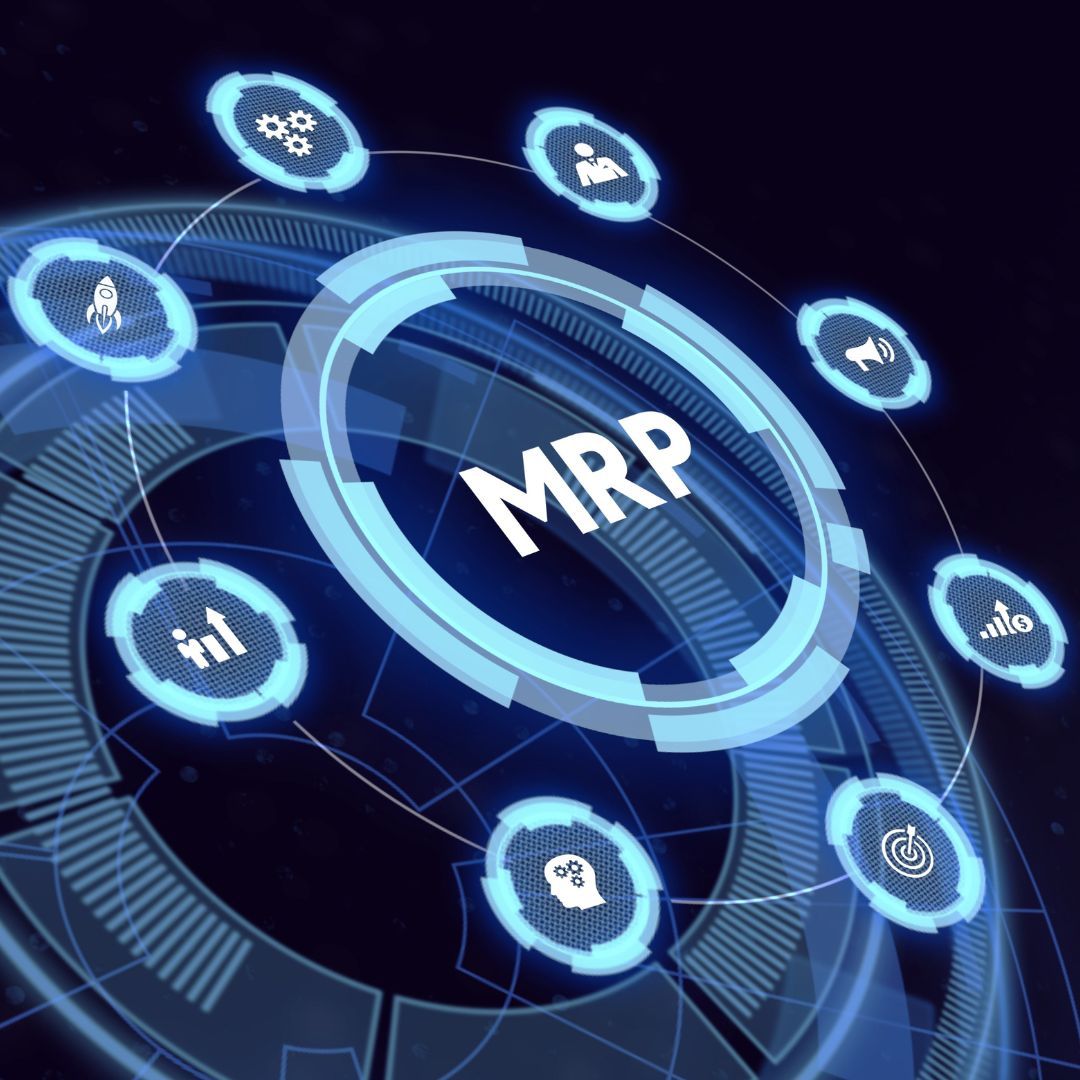
In today's rapidly evolving manufacturing landscape, efficient supply chain management is essential for ensuring timely production and meeting customer demands.
Material Requirements Planning (MRP) is a powerful tool that assists manufacturers in optimising their inventory levels, scheduling production, and maintaining a streamlined production process. This article aims to provide a comprehensive guide to MRP, focusing on its key concepts and highlighting its benefits.
Understanding Material Requirements Planning
Material Requirements Planning is a software-based system that helps manufacturers determine the necessary quantity and timing of materials required for production. By analysing various factors such as sales forecasts, inventory levels, lead times, and bill of materials (BOM), MRP enables manufacturers to efficiently plan and control their production and inventory management processes.
Key Concepts of MRP
Bill of Materials (BOM): A BOM is a comprehensive list of components and materials needed to manufacture a product. MRP utilises the BOM to determine the exact quantities of materials required for each assembly or sub-assembly.
Master Production Schedule (MPS): The MPS represents the anticipated production schedule for finished goods. It serves as a foundation for MRP calculations, enabling the system to calculate the quantity and timing of materials required to meet the production targets.
Inventory Management: MRP provides real-time visibility into inventory levels, helping manufacturers avoid shortages or excesses. By monitoring inventory levels and analysing demand patterns, MRP ensures optimal stock levels, reducing carrying costs and minimising production disruptions.
Material Planning and Procurement: MRP assists in determining the timing and quantity of materials to be purchased from suppliers. By considering lead times, production schedules, and safety stock levels, manufacturers can maintain an uninterrupted supply of materials and avoid production delays.
Benefits of MRP for PCB Manufacturing
Here are the advantages of utilising MRP in PCB manufacturing.
Enhanced Production Planning
PCB manufacturing involves numerous components and intricate assembly processes. MRP optimises production planning by providing accurate material requirements, ensuring that all necessary components are available when needed. This reduces the risk of delays, minimises production downtime, and enhances overall efficiency.
Reduced Inventory Costs
PCB manufacturing often involves a wide range of components, and managing inventory levels can be challenging. MRP helps in avoiding overstocking or understocking of materials by accurately forecasting demand and adjusting inventory levels accordingly. This results in reduced carrying costs and minimises the risk of obsolescence.
Improved Order Fulfilment
By integrating MRP with customer demand data and production schedules, manufacturers can ensure timely order fulfilment. MRP assists in aligning production resources with demand, enabling faster response times, and enhancing customer satisfaction.
Effective Supplier Management
MRP facilitates effective communication with suppliers by providing accurate information on material requirements. This helps in building stronger relationships with suppliers, streamlining procurement processes, and negotiating favourable terms for the supply of materials.
Conclusion
Material Requirements Planning (MRP) is a powerful tool that brings order and efficiency to the complex world of PCB manufacturing. By implementing MRP systems, PCB manufacturers can enhance their operational efficiency, reduce costs, and ultimately deliver high-quality products to their customers on time.
M-Tek
At M-Tek Assembly we have decades of experience within the industry. We have achieved a
net-zero carbon footprint by using electric vehicles, and for every
printed circuit board we build, we plant a tree. Contact one of our SMT and PCB assembly experts today for assistance. Call
01189 455377 or follow us on
Twitter to learn more about our products and services.